产业赋能 共建AI+ 未来工厂 ——联想助力中国职业教育改革发展
当前,人工智能、大数据、物联网等技术已成为时代发展的新动能,同时,新一代信息技术成为院校人才培养的焦点。作为领先的ICT设备与服务提供商,联想在助力众多制造型企业实现数字化变革的同时,也将自身强大的技术能力与产业实践经验赋能职业教育,帮助院校提升教学与实训水平,培养高素质技术技能型人才。
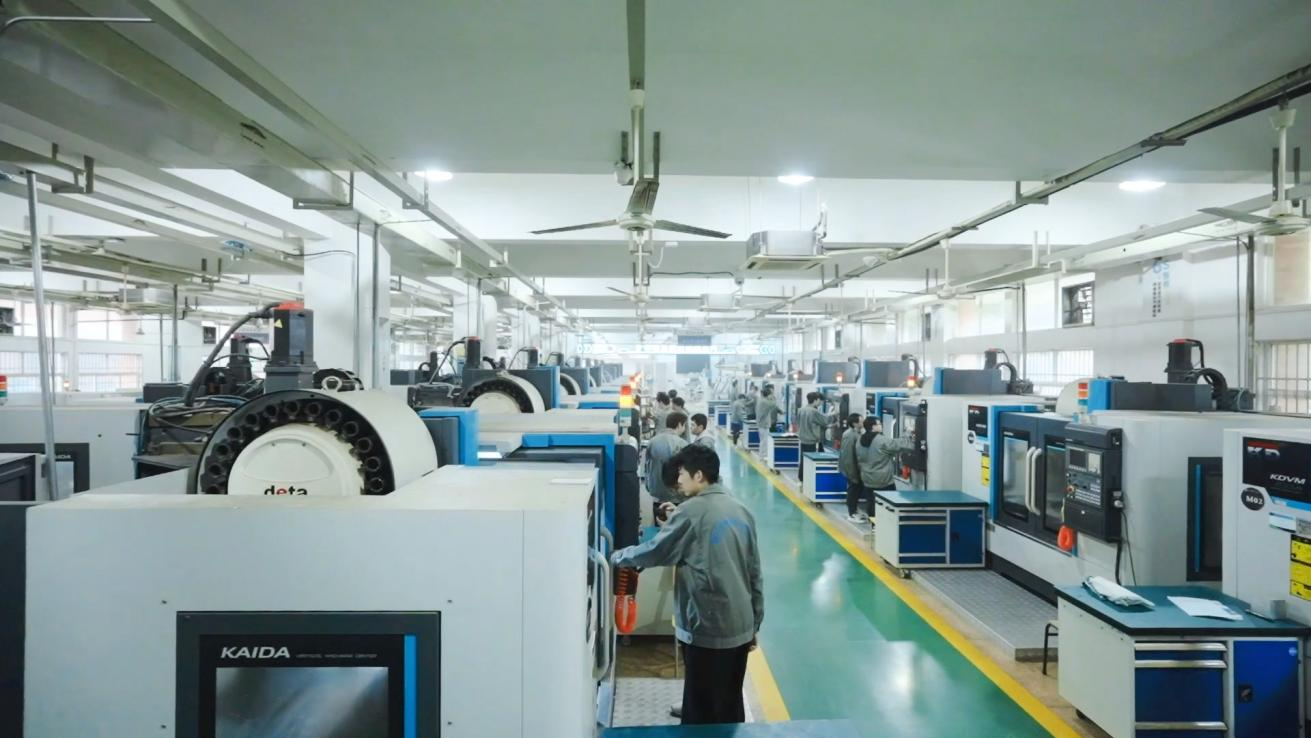
(智能制造基地)
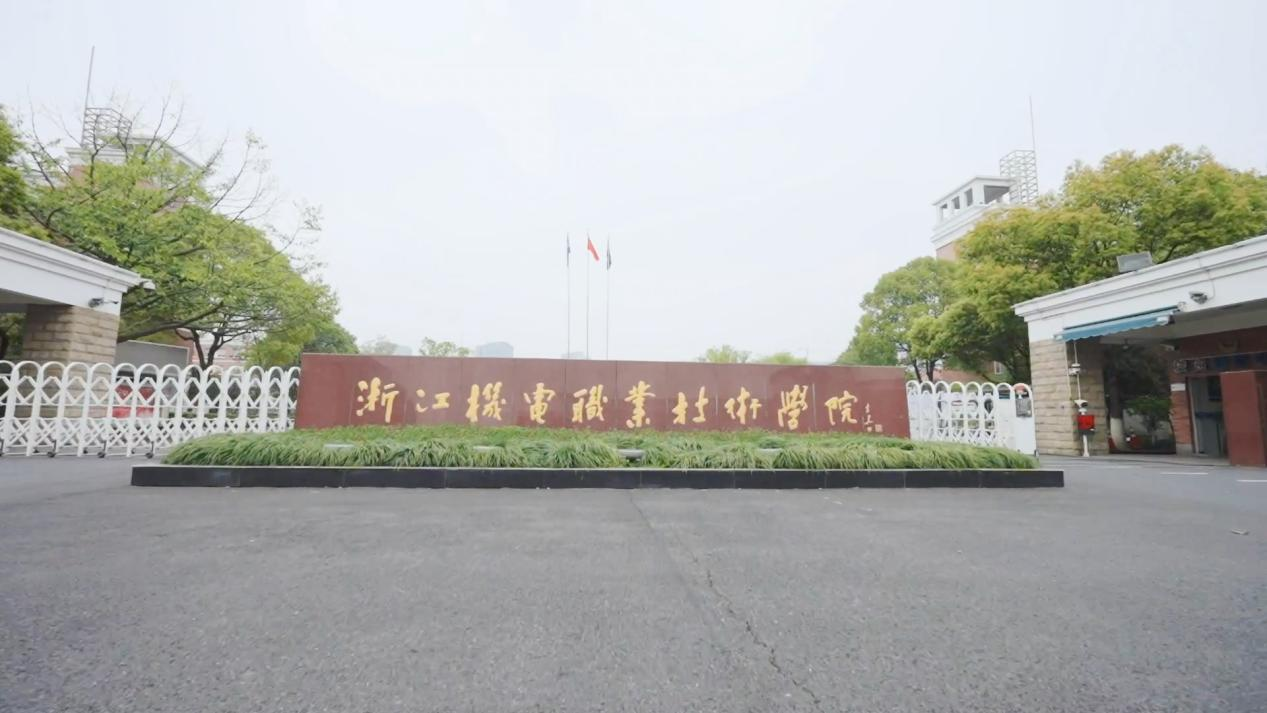
近年来,联想与浙江机电职业技术学院联合打造“线上+线下”先进的一体化工业互联网实训中心,专注新一代技术人才培育。通过联想AI+工业物联网技术,学校建立了一个全设备、全空间、全流程的工业互联网实训中心。结合数字孪生技术,将理论和实践进行线上线下虚实联动,实现了“教学、实训、科研、创新”一体化目标。
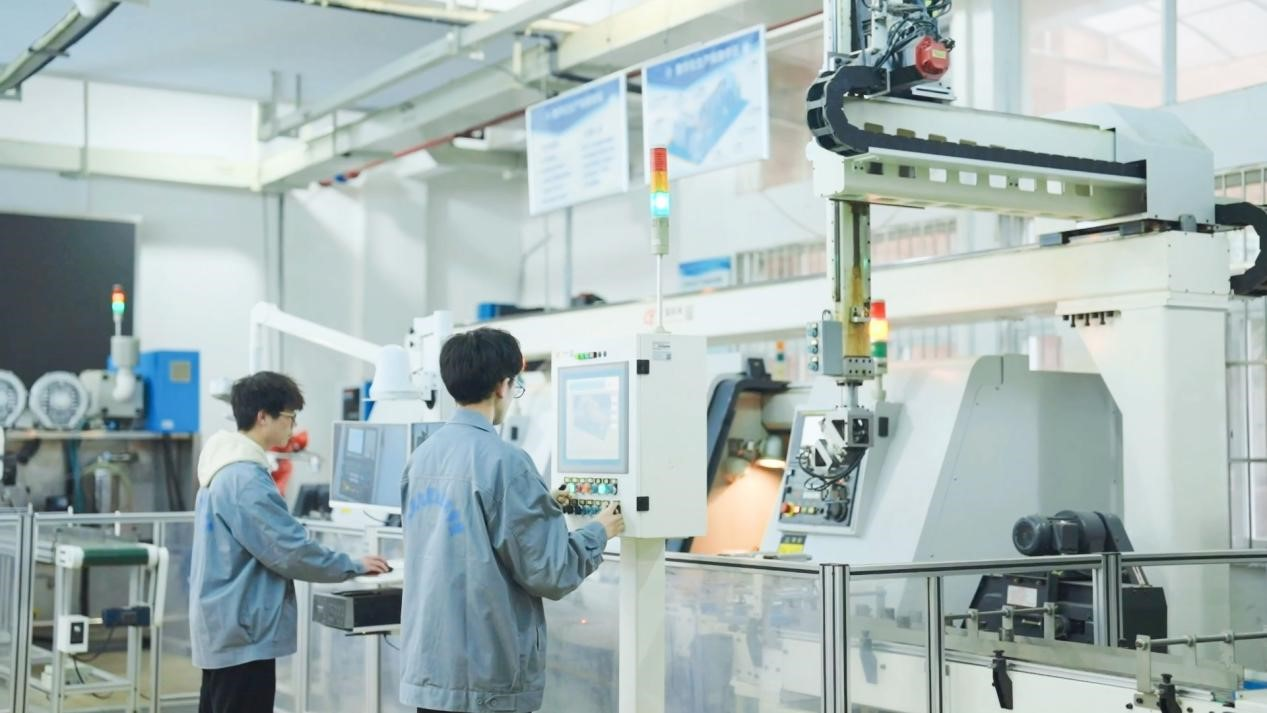
实训中心的仿真生产让学生在学校就能掌握生产全流程。 学生在实训中心扮演不同的岗位角色,按专业方向要求进行针对性技能训练,让学生成为有全局观念的“工程师”,缩短了与企业应用的距离。
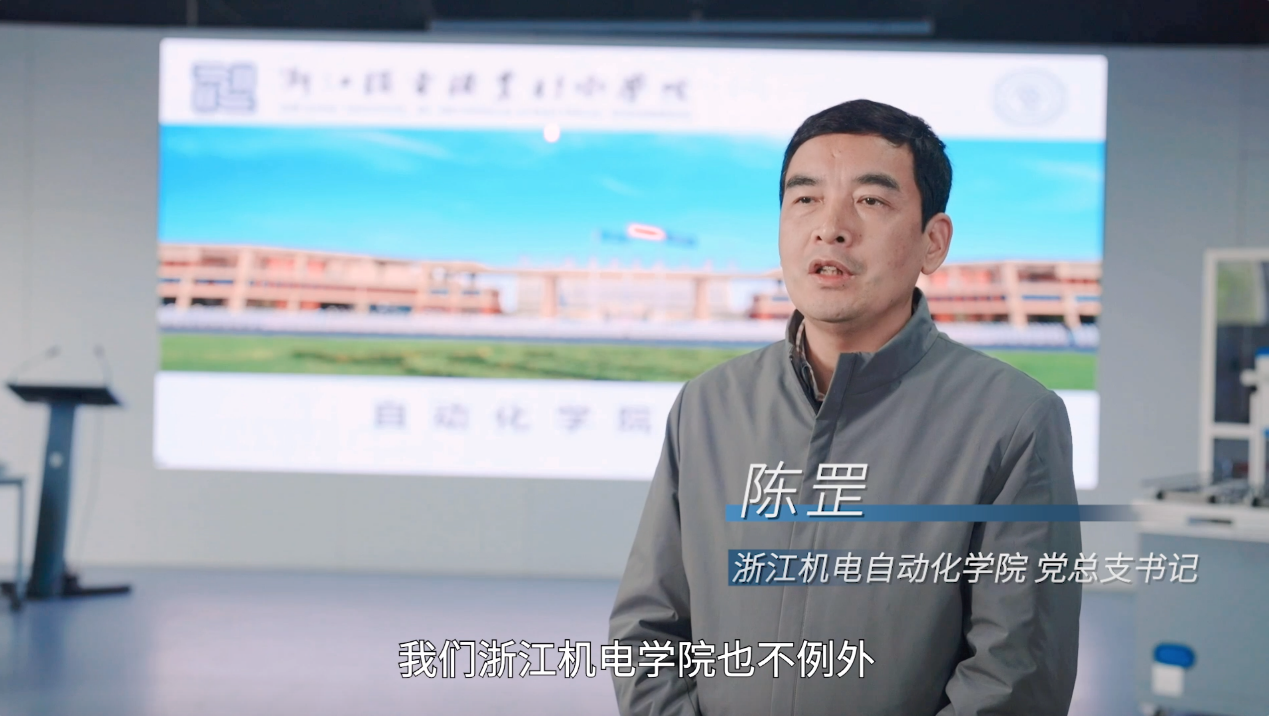
浙江机电职业教育技术学院自动化学院党总支书记陈罡表示,实训中心作为学校深化专业建设与应用的有力抓手,使得我们的职业教育特别是自动化、机电等专业实训变得更有效、更智慧和更有温度。
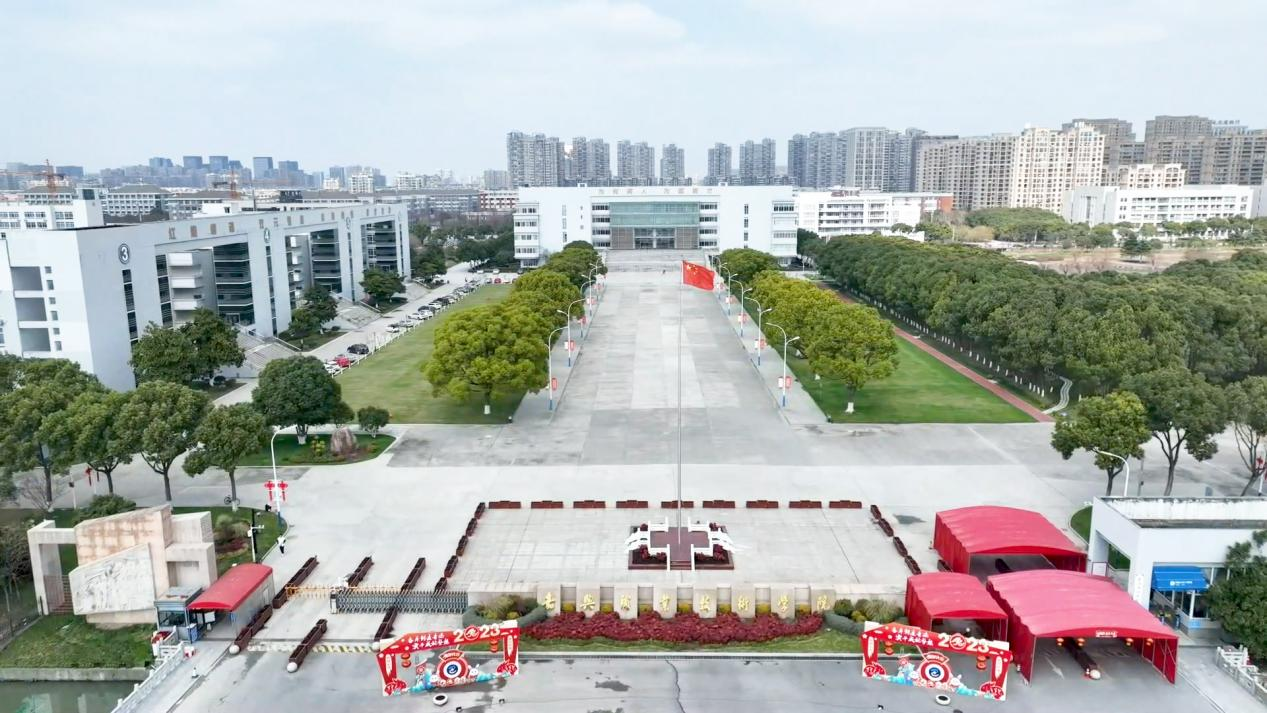
在嘉兴职业技术学院的智能制造单元数字化集成应用课堂上,副教授寇舒正在带着同学们讨论数字孪生精准定位的学习任务。
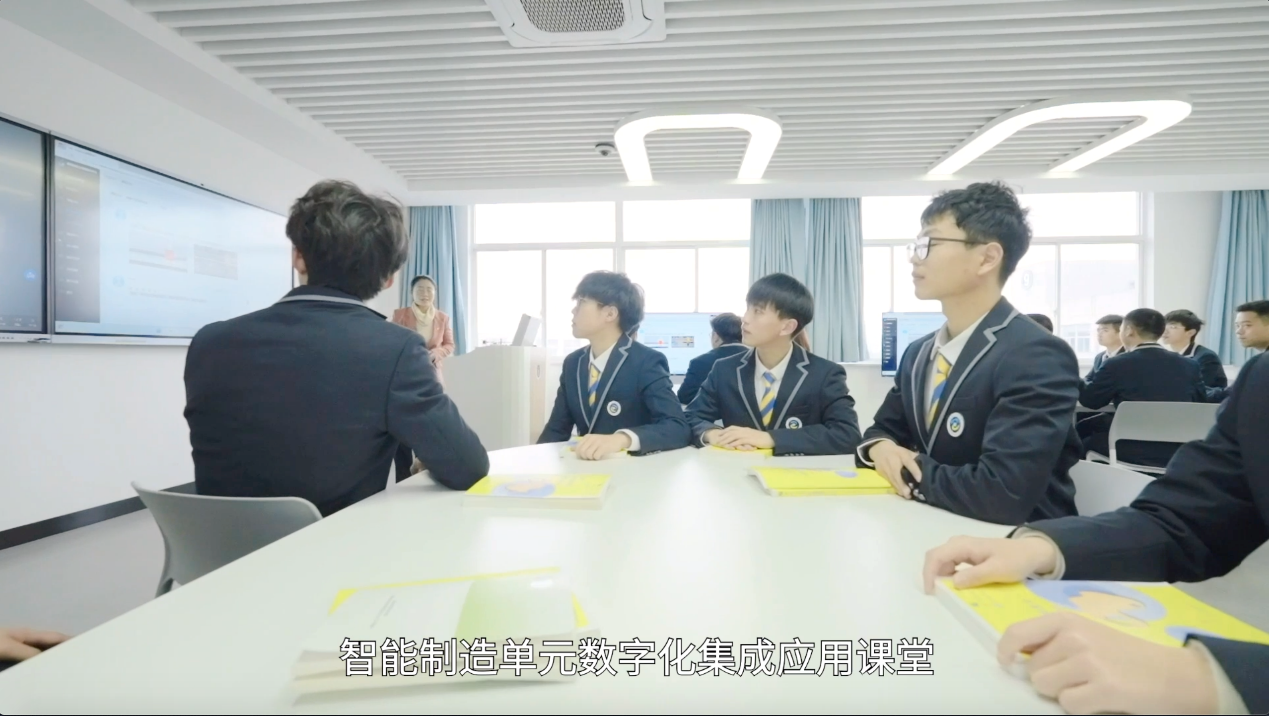
寇教授表示,当前学校的专业一直比较缺乏智能制造新技术相关的一些研究平台,传统的专业课程以经典理论学习为主,技术更新不及时,教材形式比较单一。这些摆在眼前的制约教学的“短板”时常让老师们感到苦恼。
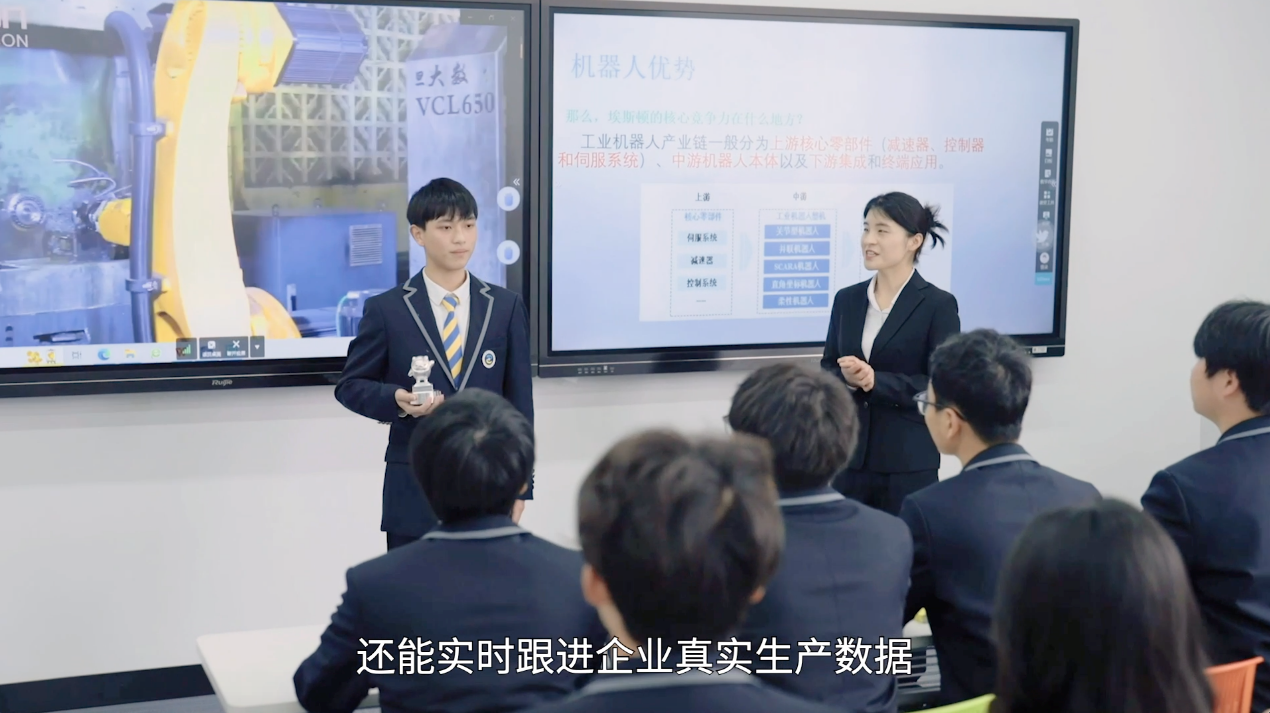
面对当前学校人才培养的痛点,联想以自身“工业互联网”技术优势,与学校开展产教融合,建设5G+未来工厂。整个实训基地分为 3 大主体功能区,分别是数字设计规划区、精密加工生产区、智能制造产线区。培养面向工业4.0+智能制造新形态、新技术、新工艺要求的高水平复合型技术技能人才。
嘉兴职业技术学院虞澄沁老师表示,自从学校采用联想工作云平台,不仅引入了数字工单,企业数字化资源,还能实时跟进企业真实生产数据,让学生吸收最新数据研究成果。联想“工业互联网”技术优势的注入,彻底改变了学生的课堂,让教和学变得生动起来,大大激发了师生课堂上的积极性。
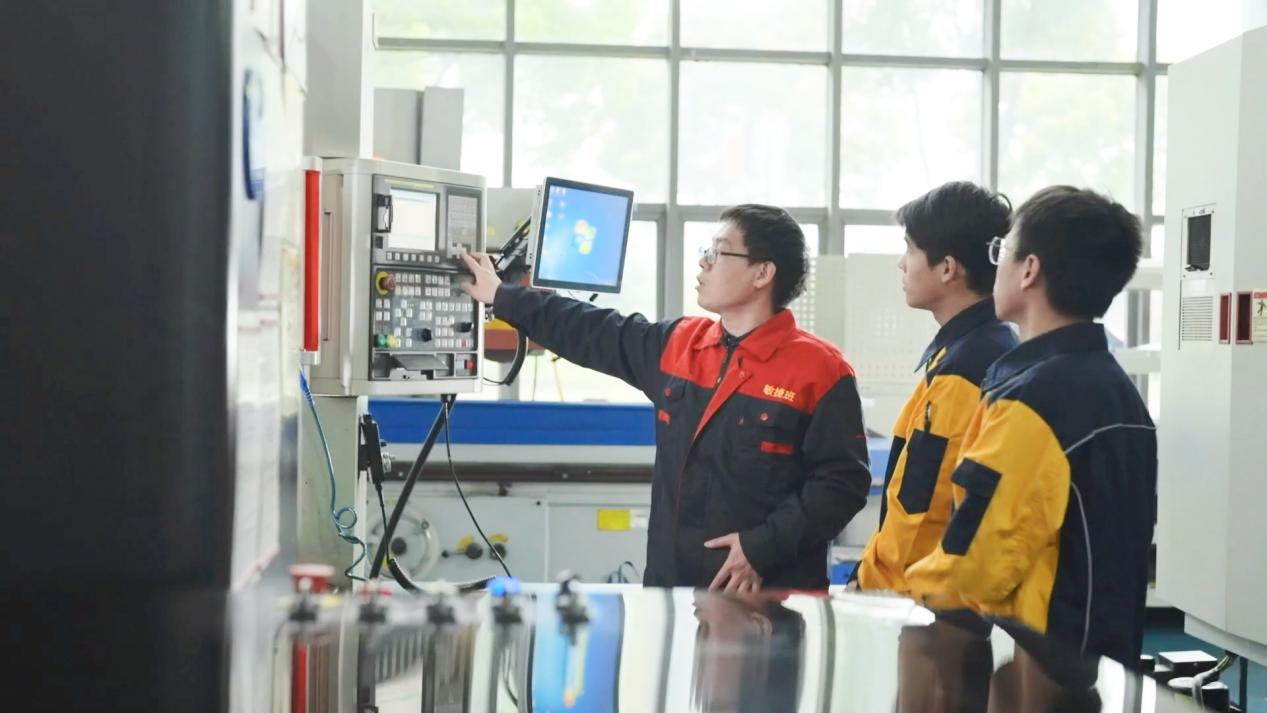
“5G+未来工厂数字车间综合实训基地”中的数字设计规划区融合了产品三维数字化设计、虚拟仿真、数字孪生、工业 5G 等新技术,通过覆盖全车间的工业 5G 网络对各工厂内的所有智能设备和云端进行实时数据交互和全流程监控,实现对产品生产制造过程的智能化管理。
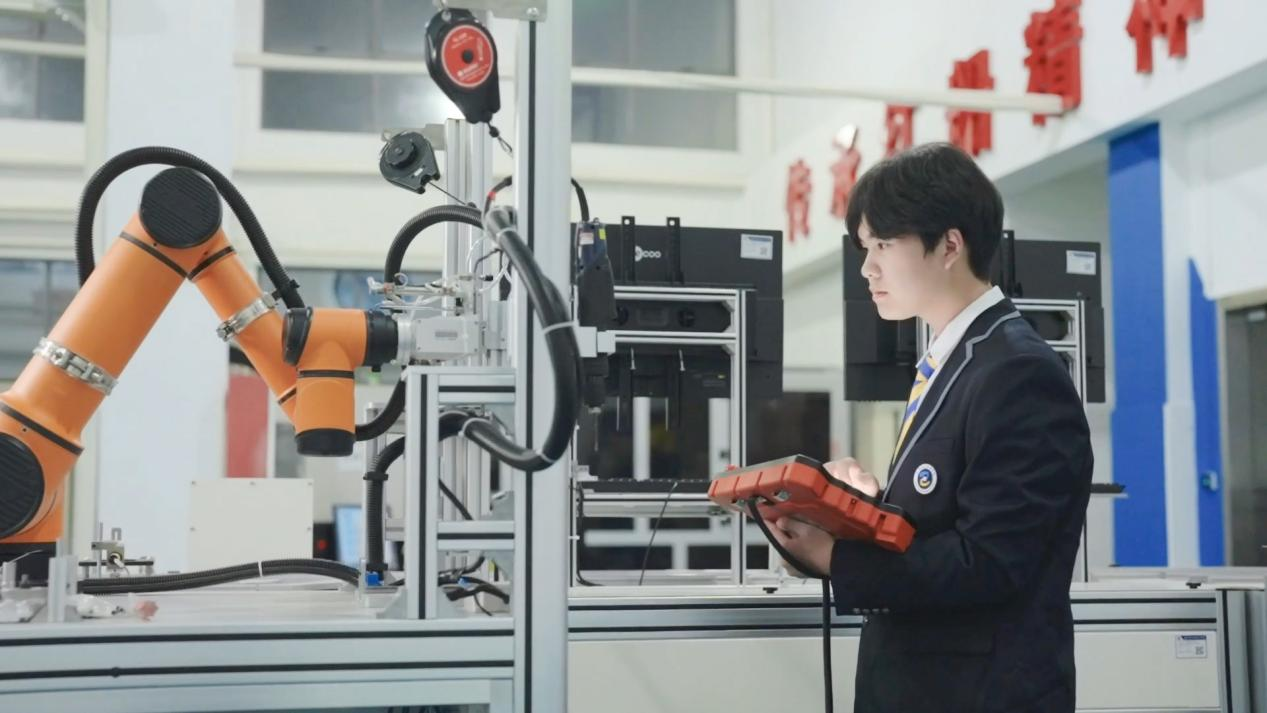
精密加工生产区由现有的7台老式加工中心数字化、智能化改造而成,通过融入信息化工业互联技术实现对现有机床的远程管控和运维。精密加工机床通过一台移动式智能工作站与新建智能制造产线建立空间连接,该工作站一体化地集成了 AGV 自动寻迹、协作机器人、3D 机器视觉、人工智能等多项先进技术,不仅能实现路径的自动规划与自主避障,还能进行物料的智能识别和自动拾取。

智能制造产线按照加工-检测-装配-包装-仓储完整流程进行设计。学生可以根据产品特性和工艺需要,全流程的进行数字化产线设计、调试和维护工作。三大主体均通过部署在实训中心内的 5G 网络与联想工业互联网云平台连接,通过 SaaS、PaaS、IaaS、边缘服务器四层架构与实训中心现场设备建立工业互联网体系,实现互通互联。除此之外,系统还配备了联想LeapLAB教学实训系统和LeapIMS数字化生产管理系统,通过电脑终端 LeapLAB 实训系统,可以直观的看到教师的开课过程和学生的实训开展过程。
嘉兴智能制造学院院长金智鹏表示,学校与联想合作建立了未来工厂,积极探索产教融合新模式,不断更新教学实训内容,着力培养高端智能制造人才,造就具有国际竞争力的大国工匠。
在探索前沿技术、创新工业互联网的道路上,联想始终坚持前研探索、科技创新。未来,联想将继续深耕工业互联网新大脑,以产业实践赋能院校AI+未来工厂反哺教育教学,探索产教融合新模式,为科教兴国战略、推动现代职业教育高质量发展贡献力量。